OZ-nology
Occasionally I get hard shifts, sometimes it’s fine. How long does it take for the relearn?
If it’s random, then it’s just the transmission relearning still. If it’s not something that you can easily capture in a log, it’s not something to worry about. It will eventually settle in. Some transmissions just take longer than others to adapt.
Relearn time can vary.
It can vary. There’s no set time frame. The system works in a continuous PID loop. Meaning that the system commands a shift, completes the shift, and measures any error in the desired target versus actual delivered shift. Then it stores that error as a correction to apply to the next shift commanded under those conditions. Then the process repeats, indefinitely, always trying to reach a correction of zero for each shift.
There are 10 gears in this transmission, and multiple drive modes. Each drive mode has its own specific transmission logic and shift schedule. Transmission functions are also based off of torque input of the engine, into the transmission. So, as you can imagine, there are hundreds, if not thousands of torque set-points that your right foot can command. These are based on throttle position, rpm, current and desired gear, and vehicle speed. So, there’s a lot of sample points for the transmission to relearn, and t can take some time for the corrections under all circumstances to get close to zero.
Now, let’s think about this from a logic standpoint. All computers are simple input-output devices once you break them down to a simple level. Meaning that for X input perform Y task. So, the programming for a computer (the tune) is completely black and white. Meaning it commands the same exact function every single time for a given input. The “instructions” for a command are exactly like I explained… “For X input : Perform Y output”. The only time that can be changed is when another system acts upon those instructions to modify that output… enter in adaptive transmission logic. Now we have “For X input : Perform Y output AND apply Y^2 correction”. Sometimes that Y^2 is exactly what’s needed to achieve the desired output, sometimes it can be too little, and sometimes it could be too much, but at the end of the day that is the only variable acting upon the base instructions. Granted, I’m explaining this logic in VERY simplified terms, but I think you can get the jest.
So, what does all this mean? It means that the simple fact that you’re experiencing these conditions randomly, tells me that it’s not tuning related. I can’t program in variable instructions for transmission logic. I program in X=Y, and every single time those instructions are needed, it is always going to be X=Y until acted upon by an external variable. If the tune itself were the issue, the problem would be easily reproducible, and would be apparent from the moment the tune is loaded, because the “base” instructions of X=Y would be incorrect. That’s not what’s happening here. The base instructions are correct, but occasionally the correction factor is not quite correct, and you’re getting an inconsistent output. Eventually the system will minimize the correction factor to zero, and you should have consistent performance under all conditions. The important thing is to not reset anything. Meaning don’t remove your tune, reload your tune, or load a different tune. Don’t rest KAM or disconnect the battery, as all of these functions can impact adaptively learned functions. All you need to do is drive the truck. The control system will take care of the rest.
Lower thermostats.
You have a lower temp t-stat installed; the fans have to be scheduled more aggressively to take advantage of the lower temp t-stat. Not really sure what the issue is, I guess.
Are you thinking that fans should run less with a thermostat installed? Because that’s definitely not the case. The only way your fans will run less is if you greatly increase the efficiency of the cooling system. By doing something like adding an over-sized aluminum radiator. Something like that would allow the system to reject more heat in a shorter amount of time, which means the fans could and should cycle less frequently.
A t-stat isn’t improving cooling system efficiency, it’s just lowering the lowest achievable temperature of the system. Meaning, if conditions are favorable the system temperature can run AS LOW AS the thermostat opening temperature. The actual operating temperature of the system under any given condition is going to be determined by the heat rejection rate of the system versus the heat production rate of the engine.
Idle issues or engine stalling
Recently, we've been getting a LOT of emails from customers complaining of idle issues or engine stalling, even check engine lights. After going through several of these complaints and figuring out the source of the issues, they have all come down to one common denominator.... Operator error. More specifically, not understanding how flex-fuel logic works when switching between ethanol-based fuel and gasoline-based fuel. So, here are some tips.
1.) The flex-fuel logic uses the fuel level input from the fuel tank as a trigger to tell the system to relearn. It needs to see an increase in fuel level of more than 10% to trigger the system. So if you're going to switch fuels, make sure that you're adding an adequate amount of fuel to trigger the logic. Good rule of thumb, add at least 1/2 tank.
2.) DO NOT leave your vehicle running while refueling. Personally, I'm not sure why anyone would do this, but to each their own. In the case of switching fuels, you MUST shut off the vehicle. Failing to do so can cause the trigger mentioned in tip #1, above, to not set properly, and thus the flex-fuel logic will not learn. Then you'll have either lean or rich DTC codes, depending on which fuel you're switching to or from. THIS ALONE has been the most common cause of the emails we been receiving. DO NOT LEAVE YOUR VEHICLE RUNNING WHEN REFULING! Got it? Good.... let's move on.
3.) Whenever you switch fuels (and you shut off the engine when refueling, right?), you should do your best to drive the vehicle immediately afterwards to allow the flex-fuel logic to learn the new ethanol content. Ideally 15-20 mins should be plenty. In "theory" the system should relearn properly, eventually, even if the vehicle is shut off prior to completing the relearn. However, in reality, it causes issues.
------Example: customer refuels at a gas station 2 minutes away from his house or work. He then drives to his destination, shuts off the vehicle, and leaves it parked for several hours. He comes back out, vehicle is now cold, and starts up the vehicle. Well, since the flex-fuel logic has not yet learned the ethanol content, the vehicle is not going to reference the proper tables for cold start, idle, etc. Also, there is a few seconds of delay from the time the engine is cranked until the O2 sensors "turn on" and begin correcting fueling. If, for example, you just filled up with E85, and didn't let the vehicle relearn, fueling is going to be very lean. The engine is going to sputter and lope and run rough and possibly even stall. You can even have check engine lights for things like misfires or system too lean, etc. The engine will eventually smooth out once the O2 sensors start correcting fueling, but of course the owner of the vehicle has already freaked out... called us 10 times, sent 7 Facebook messages, 15 texts, and posted in 5 different Facebook groups asking if his engine is blown.... I'm exaggerating for comedic effect, but you get the idea. The point is that all of the drama could easily be avoided if the owner understood how the flex-fuel logic works and gave it the proper time to work.
So, now everyone understands how the flex-fuel logic works. Spread the word. Educate others. Happy motoring!
Learning process behavior
As a general rule of thumb any “random” behavior from a vehicle after loading a tune and resetting KAM is just part of the adaptation process. Tunes, and computers in general, work in systems of “on” or “off”. That means that the values we program in the tune are specific and will command the same exact function every single time that function is commanded. That will never change. For a computer 2+2 is always 4, period.
Now, why do these trucks, and all modern vehicles have adaptive learning. That’s because unlike computers, mechanical parts don’t always perform exactly the same every single time. Wear and tear, degraded fluids, variances in temperature, even variances in tolerances from manufacturing… all can have an impact on the mechanical output from a component. So, for example, even though the PCM is commanding 2+2=4; the transmission might end up outputting 2+2=3. I’m of course explaining this in very simple terms as the actual logic is much more complex than this explanation. So, if the PCM wanted 2+2=4 and instead the transmission delivered 2+2=3, the PCM has memory banks where it stores this error percentage, and the next time it commands 2+2, it will apply that stored error to the command to try to reach its target value, 4, in this case. That “loop” of “command > measure error > apply error > command again” runs over and over and over, indefinitely, with the goal of reaching a measured error of “0” for all commands. Obviously, that will never be possible since there will continue to be wear and tear on the vehicle as it’s driven, so there will always be some form of adaptive learning taking place.
Ideally, the adaptive corrections will be small and mostly imperceivably, and as long as there are no major mechanical defects, they will always eventually reach that point. However, in the case where you have loaded a tune, you are now asking the mechanical components of the vehicle to perform in a manner that they were not previously performing. Combine that with the fact that you are clearing all of those adaptively learned functions that have likely been learned over thousands of miles of use. So not only are we asking the transmission, for example, to behave differently, we’re also clearing out all of the “corrections” the PCM has learned which take into account various wear and tear or other variances for your specific vehicle, and all of that has to be relearned. So, it’s not very reasonable to think that your transmission, is going to shift 100% perfectly in a couple hundred miles, when it took thousands of miles for it to learn what you just cleared out of its memory banks. This situation is exponentially worse on a vehicle with higher mileage as they generally have much more wear than lower mileage vehicles, and the tolerances from that wear must be accounted for via adaptation. This adaptation only takes place as the command is completed and error is measured. So, in the case of transmission adaptations, there are literally hundreds, and in the case of 10 speed trucks, thousands, of possible shift commands with the major influences on those commands being pedal input, vehicle speed, and gear pairing. So, there is an enormous amount of data that your vehicle must relearn to reach that point of “0” measured error.
Though it’s common for tuners to recommend a certain number of miles to allow adaptive learning to take place, in reality that’s just the tip of the iceberg. Fifty miles, for example, should be enough time that the adaptives should have brought any large corrections down to a range that should not cause issues when driving the vehicle, but the actual relearn process is far from over in 50 miles and in reality, miles are irrelevant in terms of adaptation or relearn. What matters really is drive cycles and how many times a specific command was completed. For example, loading your tune and then jumping on the highway and driving for 100 miles would do pretty much nothing in terms of transmission adaptations. This is because at highway speed there would be very few, if any, transmission commands occurring. The transmission needs to command and complete functions to adapt properly.
With all of that being said, that doesn’t mean that it’s not possible for a certain behavior from a vehicle, after loading a tune, can’t be tune related. A good rule of thumb for determining what might or might not be tuning related would be asking the questions; “Is this behavior easily repeatable and easily duplicated?”…. “Is the behavior consistent and negatively impacting my driving experience?”…. “If asked to, could I easily record this behavior in a datalog?”….. If the answer to those questions are mostly yes, then it would be a good idea to contact your tuner and discuss the issue and/or offer to datalog the problem. If the answers to these questions are mostly no, it would be best to just drive the vehicle for more time, monitor the behavior, and see if it improves. In most cases, the behavior will improve with more drive cycles and adaptation.
The guy building my motor said that whoever tuned the truck put a bad tune in it that caused detonation and sent me this picture any idea why this happened?
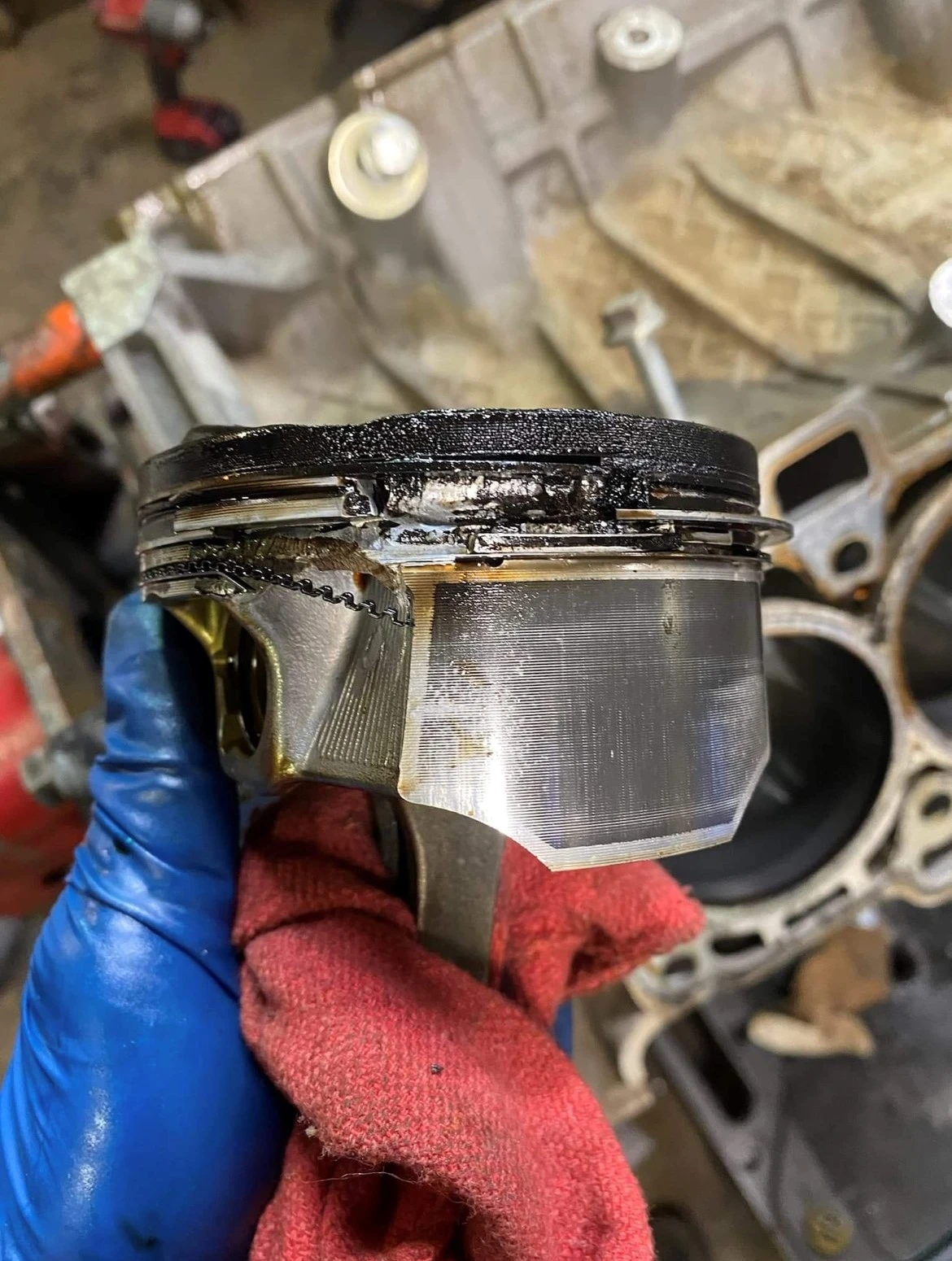
"Spark knock?"
Today, we talk about the Gen 3 Coyote "rattle" that is VERY commonly confused for spark knock. While this is more common on the Gen 3 engines, the phenomenon can occur with any generation of Coyote engine, and really, any engine that uses Variable Valve/Cam Timing.
First things first.... https://www.youtube.com/watch?v=FWXdISsxrlw
The robo-naration in this YouTube video is awful, but it does an excellent job of explaining how Ford's TiVCT system functions. Understanding how the system functions is integral to understanding the source of this noise. So, watch the video if you want to truly understand what's going on.
As for the noise, it isn’t spark knock. It’s a combination of several things, but it has nothing to do with spark knock. For one, spark knock wouldn’t be as loud as the noise these trucks typically make under these conditions. The only way spark knock would be audible on one of these engines would be if the knock sensors were completely non-functional. If that were the case there would be check engine lights on for the knock sensors being off-line. The knock sensors are MUCH more sensitive than human ears, and register possible engine knock well before it ever reaches the point of being audible.
The noise originates from the VCT system. It’s coming from the cam phasers and being transmitted through the timing chains and the rest of the timing components. The noise happens when oil pressure and flow to the cam phaser is not substantial enough to overcome the inertia of the cam rotation. Time stamp 1:40 in the video illustrates this really well.
The VCT system is attempting to apply oil pressure to the internal passage inside the cam phaser (vanes), and that pressure is what retards the cam timing in relation to the crankshaft rotation. If the oil pressure/flow is not substantial enough to overcome the force of the cam rotation. The oil will be pushed back out of the cam phaser and the oil will back-flow through the VCT solenoid. When this happens, the vanes inside of the cam phaser will “rattle” back and forth until oil pressure/flow is enough to overcome the rotational force of the cam. THIS is the source of the noise that everyone reports with these engines.
As mentioned, the noise occurs when the oil filling the voids in the phaser can’t overcome the force applied by the rotation of the cam and the oil is pushed back out of the void in the phaser and the vanes inside the phaser rattle. That noise can then be transmitted through all of the timing components, including the timing chains, causing the chains to "slap" against the timing chain guides.
This issue seems to be more prominent on Gen 3 engines versus Gen 1 and 2 engines. This is likely due to the stiffer valve springs that the Gen 3 engines use. Also, Gen 3 engines have a High-Pressure Fuel Pump (HPFP) for the direct injection system, that is driven off the passenger side exhaust cam. The HPFP and stiffer valve springs increase minimum force required to rotate the cam phasers, considerably, compared to older generation Coyote engines. That is one of the reasons this noise doesn't seem to be as prevalent in the previous engines. The evidence of the higher loads on the VCT phasers is also evident in the stock calibrations, as the Gen 3 engines require considerably higher duty cycles from the VCT solenoids to achieve similar degrees of cam retard, compared to Gen 1 and 2 engines.
The noise typically only happens at low RPM because the oil pump is a positive displacement design and can only displace a fixed volume of oil with each revolution. This means that to increase oil flow, volume, and pressure the pump requires more RPM. It should also be noted that pressure is a measurement of RESISTANCE, and in the case of an oiling system, it is a measurement of resistance to oil flow. Pressure increases when the total volume of oil flow exceeds the requirements of the engine. Meaning, the oil volume is sufficient to fill the voids in the engine left by things like bearing tolerances, cam journal tolerances, etc... and the oil system is meeting those requirements and providing a surplus of oil volume, and thus there is resistance to flow and pressure increases. This is why we expect oil pressure to increase with engine RPM. For those paying attention thus far... the light bulbs should be going off in your head. We've determined that the phaser rattle is caused by a lack of oil pressure/flow and now, we've also determined that oil pressure/flow is at it's lowest when engine RPM is low. Ding... ding... ding.... perfect recipe for cam phaser rattle. This is also why the noise is typically only heard for a split second on throttle tip-in, as right after that point oil pressure is able to meet the requirements to achieve the target cam angle and the rattle stops. However, the fact that the noise typically only happens on tip-in is one of the main reasons it's confused with spark knock.
Alright..... so now we've established the cause of the noise and we've covered how to stop the noise.... So how do we put this into practice? Well, we've already covered that increasing oil pressure will help with the issue. We know that increasing engine RPM will increase oil pressure, but how can we increase oil pressure if increasing engine RPM isn't an option?
The easiest way to do that is to run a heavier weight oil. The heavier weight oil will automatically increase oil pressure. Now, there is a limit. You can't go fill your engine with 90w gear oil and think everything is going to be fine.... as the trade off to heavier weight is a slight decrease in flow. So we have to balance the oil weight versus the engines oil flow requirements. That being said, this has been tested over and over in the Coyote engine, and it's been found that running up to 5w50 weight oil is safe and effective at increasing engine oil pressure. We use, and recommend 5w50 weight synthetic oil (please don't ask me for a specific brand, as I don't have one).
Also it is recommend to over-fill the oil pan by ½ quart, on any Coyote engine that is going to be ran hard. As most experienced Coyote engine builders will tell you, these engines have issues with oil drain-back under high load and RPM. Adding and additional 1/2 quart increases capacity to prevent oil starvation under extended load, put is not over-filled to the point that it could cause issues with windage. So, if you're running your truck hard, consider 5w50 and 1/2 quart overfilled.
To be VERY CLEAR.... I'm not saying that changing to 5w50 oil is magically going to make this noise go away. What I am saying is that it does help the cause of the issue, and for some it has pretty much resolved the noise.
LOOOONNNGGGG story short, the noise is not spark knock. Running heavier weight oil can improve the issue, but is not a "fix". There are tuning changes that can be made, which we've been including in our tunes for a long time now, that also can improve the issue, but at the end of the day... while it is annoying, Ford doesn’t consider it detrimental to the health of the engine. So, take that for what it's worth to you.
Can we PLEASE stop calling this "spark knock" now??
Will an upgraded Heat Exchanger improve temps?
______________________________________________________________________
The heat exchanger is larger than the Whipple exchanger and can help to control temps, but larger HE’s generally improve recovery, after the pull. They don’t help much with temperature rise during the pull. That’s more controlled by the size of the intercooler “brick” below the blower. If the larger HE helps to lower base system temps, then it will improve the temps through the pull.
Tunes do not suddenly go bad.
We get emails from time to time from customers that have had a tune installed, typically for a good amount of time, and they recently are having some sort of mechanical issue. I like to affectionately refer to this as joining the "Ever-Since" club, because they think that "ever since" they loaded a tune that whatever happens to the vehicle must be because of the tune. I'm joking, of course, but it is a common enough question, that I figured I would give an explanation for everyone, as I'm sure not everyone fully understands how tuning, or really computers in general, works.
This is an email response to a customer that has had his tune installed for just about two years, and recently started having weird shift behavior from his transmission. So, the response is geared towards that specific situation, but the concept applies to any vehicle function or system, and how a tune can or can't cause a problem.
===========================================
Alright.... so, this is a pretty common question. Common enough that I'll probably make a post about this in our Facebook group. Let me break it down for you.
Tunes are computer programs. Right? Computers are logic devices. That means to a computer yes is always yes, no is always no, 1 is always 1 and 2+2 always equals 4. So, a computer is going to perform the same actions, when commanded to do so, and will perform them in the same exact manner, every single time, forever, or until the programming is modified by an external source.
So, what does that mean? It means that in the last almost two years that you've had your tune installed, the tune has been commanding your transmission to shift exactly the same way.... every.... single.... time. It didn't change. The only way the tune changes is by over-writing the program with a different program. So, if you didn't do that, then the tune didn't change. That means, that if the tune were the cause of your current issues, it would have started basically immediately after loading the tune. Why? Because for it to exhibit this behavior, the programming would have to be incorrect from the beginning if the tune were causing the behavior, and since you're just contacting us now about this, I'm going to assume that your transmission wasn't behaving this way for the last two years.
Now, we know the programing (tune) didn't change. So, what did change? Well, just like any mechanical equipment, your transmission, along with every other part on your truck, wears over time. Now, there are adaptive functions built into the vehicle's control system that can account for some of that wear, especially when it comes to the transmission, because transmission parts are designed to wear out over time. That's just the nature of them. Automatic transmissions use internal clutches and friction plates, and just like a clutch in a manual transmission, they wear out over time. They're wear items, and at some point, will have to be replaced. The adaptive functions in the control system can adjust and offset some of the transmission pressure functions to account for clutch wear, but eventually the wear can reach a point where the adaptive logic can no longer account for the added wear, and you can experience drivability issues or random behavior. Also, it's possible for other parts or sensors of the transmission to wear out, break, or reach the end of their service life, and any of those situations can cause issues as well.
Now, which of those potential issues are the cause of your symptoms? I can't say, as it would be impossible for me to diagnose something as complex as a transmission via email. However, what I can tell you is that your tune isn't the cause of your problems, nor is it going to be the solution. This is a hardware issues, and you can't fix hardware with software. So, as you already eluded to, I think it's time to service the transmission.
===========================================
So, to summarize..... Any easy "litmus" test that you can do when determining if the tune is the cause of whatever problem the vehicle is exhibiting, is just to ask yourself. "Did I just install/change my tune?" If the answer is no, or I'll even go as far to say if your vehicle has been running fine for at least a week after loading a tune, then chances are pretty good the tune is NOT the source of whatever is going on with the vehicle and you should follow typically troubleshooting procedures, as if the vehicle was not even tuned.
Hopefully this helps, and maybe can save someone some time if they're trying to diagnose a mechanical issue.
Why we recommend to upgrade to Stage 2 throttle body.
Catalytic converters abuse
I made a similar post in our F150 group a while back, but seeing several posts recently from trucks losing engines, I though maybe this PSA might help save someone a potentially expensive failure.
Let me be blunt.... Boost doesn’t kill cats, abuse kills cats. There are literally hundreds of different forced induction engines produced by various OEM's, and you don't see those engines blowing up and eating cats every day. So, boost isn't the issue here.
Things like hot-lapping at the drag strip, long pulls up steep grades, excessive high speed highway pulls, and back to back roll racing are all common causes for damaged cats. Stock cats are actually very resilient, if they aren’t abused. However it doesn’t take too many overheating cycles for the catalyst to break down, become brittle, and break apart and/or collapse. If that happens, the exhaust becomes blocked and the increased back pressure caused by the clogged exhaust will cause cylinder pressures to sky-rocket, leading to engine damage. Cheap "high-flow" cats are even worse as they are typically made from a metal substrate that is even less resistant to heat, and they will actually become molten, and the melted metal will clog the exhaust almost completely. One key thing to pat attention to, that might save your engine, is if the truck feels down on power and/or if the exhaust note changes suddenly. If either of those occur DO NOT drive your truck aggressively, and service the truck ASAP.
There are protections in place to try to keep the catalysts from overheating. People refer to that logic by many names, but the most common is “cat protection”. What the logic does is enrichens the mixture (makes the AFR richer) to lower exhaust gas temperatures (EGT’s) in an attempt to lower the catalyst mid-bed temperature. This works, so long as the protection logic is only active for a short period of time. The issue comes when the logic is active for longer periods of time, or with greater frequency. This is because the enrichment (fuel) that is used to lower the exhaust gas temperatures is a bit of a double-edged sword. Yes, the added fuel does lower EGT’s, but that added fuel also creates a chemical reaction inside the catalyst, as removing excessive hydro-carbons from the exhaust is the job of a catalyst. That chemical reaction will cause the catalyst to actually heat up further, and this is what typically damages cats.
So, how do you reduce the chance of failure? Simple... don’t abuse the cats.
Now, that doesn’t mean you can’t enjoy your truck. It means that WHEN you enjoy your truck and the added power, you also need to give the cats adequate time to cool off before abusing them again. The mid-bed temp is the critical part, and as you probably already guessed, mid-bed refers to the center area of the catalyst. That area takes much longer to regulate heat than the external parts. A good analogy would be a hot-pocket that you just pulled out of the microwave. If you let it sit for a couple minutes, the outside is cool enough to touch, but when you bite into it, you melt the flesh off the roof of your mouth. Your cats are the same way. The mid-bed holds heat much longer than the rest of the cat, so it needs adequate time to cool off.
The best way to let your cats cool off is to just cruise. Cruising at highway speeds does two things. One, AFR’s are in an ideal range for lower EGT’s without the added fuel that could cause chemical reactions and heating, and there is adequate exhaust flow to move the cool exhaust through the catalysts to further lower the temps. Also, you have the benefit of ambient air passing over the external portion of the cats, which will further lower temperatures, and as the external portions of the cats cool, they will act as heatsinks, pulling heat form the mid-bed of the catalyst. The issue is that heat is generated in the cat at an exponential rate, but it’s removed from the cat in a much slower logarithmic rate. So, it’s very easy to over-heat the cats if you don’t consciously try to take care of them.
There are catalysts available, like Gesi cats, that are designed to handle more heat than stock converters, while also increasing flow as well as improving performance, but even those cats can be damaged if they are abused. Hopefully this post will give a better understanding how cats work and how the protection logic functions, and in-turn maybe prevent someone from having a catastrophic engine failure.
~ Ken Osborne